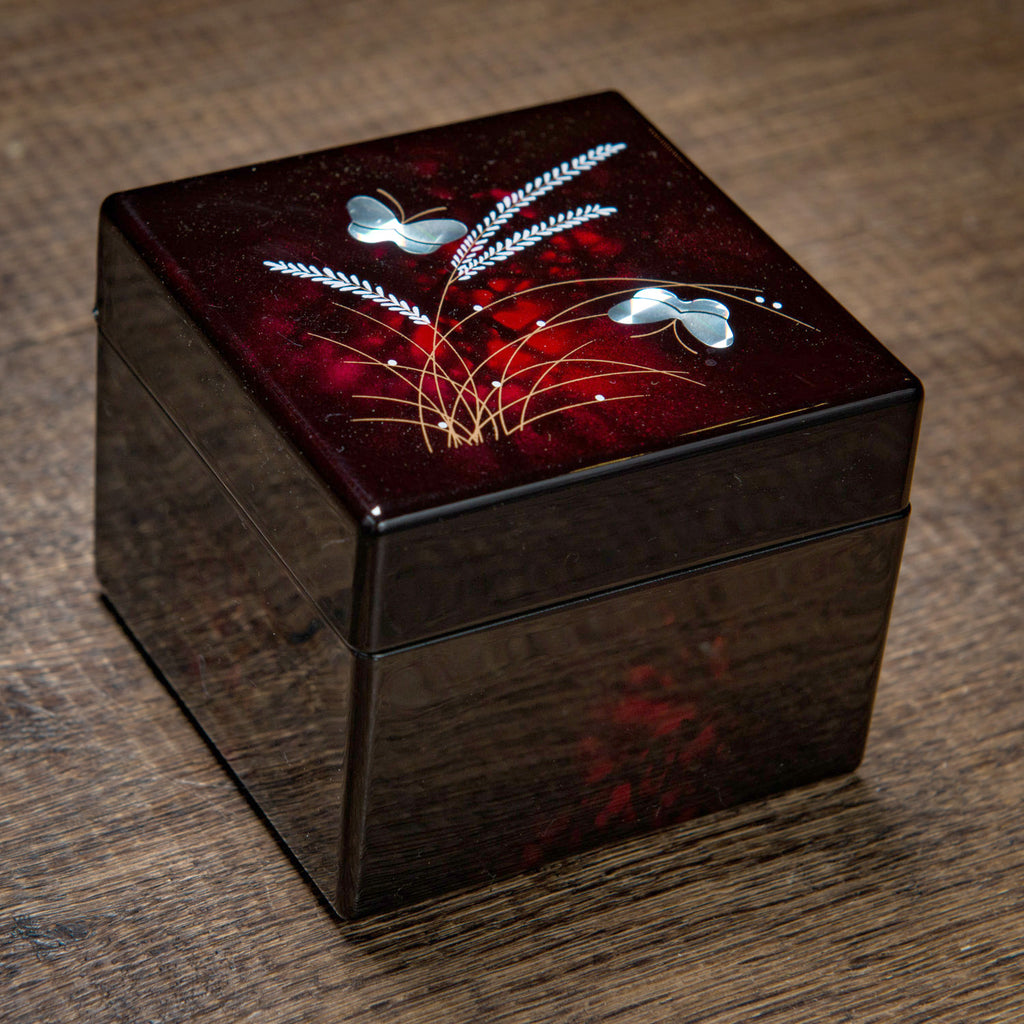
Japanese Lacquer Work
Japanese Lacquer Work
Japanese lacquer work can be seen on a huge variety of decorative interior objects, including paintings, prints, furniture, boxes and bowls. Characterised by its beautiful high-gloss finish, the lacquer is applied to several different materials including wood, silk, metal and plastic, usually over a black or red undercoat.
What is Japanese Lacquerware Made Of?
Japan's lacquer contains the highest proportion of urushiol, the substance that gives lacquerware its coveted properties. The sap from the urushi or lacquer tree has been used in Japan since prehistoric times, when it was used as an adhesive for mending pottery and fixing arrowheads to their shafts.
Lacquer itself is clear, and one style of Japanese lacquer work involves no added pigment at all, leaving the colour and grain of the wood to speak for themselves. However, more often base coats of black and/or red are applied. Usually the base is painted black then covered with coats of red, which is then partially polished away. This leaves the black undercoat showing through in places, creating a stunning two-tone sheen.
Traditional Japanese Lacquer Techniques
The production of Japanese lacquerware is traditionally a complex process involving multiple layers and specialist techniques. The stages in this process are roughly as follows:
1. Priming the wood
Before the lacquer can be applied, the wooden core undergoes a long process of shaping and seasoning. This creates a stable base, which is then impregnated with raw lacquer to make it waterproof and prime it for subsequent coats of increasingly refined lacquer.
2. Applying the lacquer
Each coat is hardened before it is polished and the next coat applied. This involves placing each freshly coated piece in a specially controlled environment of high temperature and humidity. It can remain there for up to several days, during which time a number of chemical processes take place, causing the lacquer to harden whilst maintaining a high moisture content.
3. Polishing
After hardening each coat is polished using various abrasives, ranging from powdered stone to crushed flower petals. When the object has taken on a silken smoothness and a high lustre, it is ready for decorating.
4. Decoration
Sometimes the object is left as it is, without any ornamentation to interfere with its natural elegance. Often, the surface is painted with delicate designs in variously coloured lacquers, sometimes to complement a relief carved into the base. Other times, a design is cut into the hardened layers of lacquer then filled with colour or precious metal.
In the style known as maki-e, an illustration is created by applying gold, silver, tin or mother of pearl in leaf, flake, or powder form. This is sprinkled over the decorative lacquer while it is still tacky to create an opulent metallic sheen.
5. Finishing
The final step in Japanese lacquer work is the application of the clear top coats. Not even a speck of dust can be allowed to touch the surface as the last coats of lacquer are applied and hardened, hence the Japanese saying, "urushi should be applied in a boat at sea".
Lacquerware continues to interact with its environment long after the production process. In climates less humid than Japan's, it is recommended that you store lacquerware next to an uncovered glass of water to preserve its moisture content. Minimising its exposure to light will also help prevent discolouration.
The Japanese Shop supplies a variety of beautiful Japanese lacquerware gifts, including bowls, jewellery boxes, bento boxes and more. Browse the range here and order online today.